Entendendo o Lean
Primeiramente veja abaixo as principais ferramentas do Lean em um desenho que facilitará a compreensão da mentalidade Lean, em seguida algumas de suas ferramentas.
Casa Lean
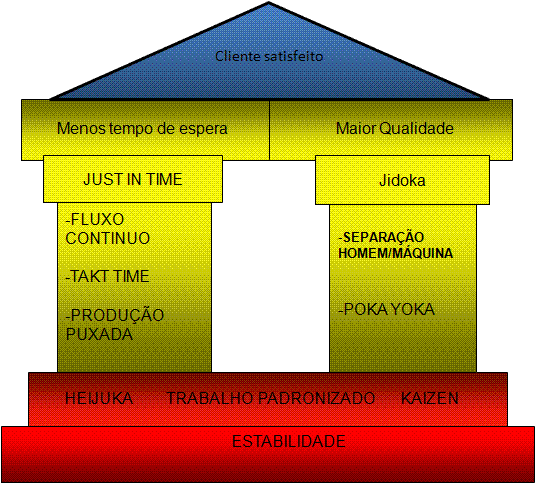
LeanTools (Ferramentas do Lean)
1- VSM Mapeamento do Fluxo de Valor
2- TPM Manutenção Produtiva Total
3 - Qualidade na Origem
4 - 5S
5- Gestão Visual
6- Trabalho Padronizado
7- SMED Redução do Setup
8- Redução da dimensão do Lote
9- Produção Celular (em fluxo contínuo)
10- Takt time Balanceamento da produção
11- Nivelamento e alisamento da produção
12- Sistemas
13- Kanban Sistema puxado
14- Kaizen Melhoria contínua
1- VSM Mapeamento do Fluxo de Valor
O mapeamento do fluxo de valor nada mais é uma representação visual dos fluxos de materiais e informações para cara processo ou produtos. Serve para analisar e identificar cada passo do processo e assim criar um plano de ação para otimizar.
O processo de mapeamento é uma etapa inicial crítica, pois é a partir dela que se desenvolve a aplicação das técnicas lean. Assim, o mapeamento ajuda a evitar o erro comum de selecionar ferramentas isoladas.
O ciclo de mapeamento inicia-se com o levantamento do estado atual. Então, rapidamente, um estado futuro é projetado, tendo como essência os princípios lean. O passo seguinte é elaborar um plano de implementação para alcançar o estado futuro.
Acompanhar e compreender o processo da fábrica para facilitar, eliminar os desperdícios e suas fontes .
Localizar os gargalos, identificar a melhor ferramenta a ser implementada e priorizar a melhoria.
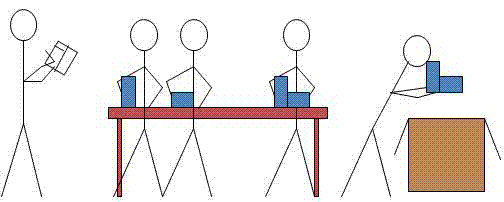
2- TPM Manutenção Produtiva Total
A Manutenção Produtiva Total nada mais é um conceito de trabalho que quebra o paradigma que durante décadas imperou nas indústrias: um operador de máquinas e equipamentos somente opera máquinas e equipamentos. A ferramenta TPM nos ensina que o operador de máquinas e equipamentos também torna-se capacitado a executar manutenções mecânicas e elétricas, sendo capaz de perceber alterações no equipamento antes que este quebre, minimizando o tempo de parada de máquinas para manutenções corretivas, aumentando o tempo produtivo das mesmas.
Podemos perceber o aumento da eficiencia do colaborador o mesmo sente-se responsável pelo equipamento, trata o equipamento como algo de sua propriedade, é perceptivel a responsabilidade do mesmo para com o equipamento.
Os benefícios da implantação dos conceitos de implantação da TPM são claramente visíveis: o tempo de parada de equipamentos por quebra diminui, os custos associados a estas paradas também diminuem, aumentando, por conseguinte, a capacidade produtiva da fábrica e a possibilidade de aumento de receita e das margens dos produtos manufaturados.
*Fazer manutenção preventiva nas máquinas para evitar a parada da linha de montagem e garantir a qualidade dos produtos.
*Criar um sentimento de posse do operador com a máquina, evitando alguns descuidos com a máquina deixando o operador como responsável da mesma.

3 - Qualidade na Origem
O Poka Yoke é um termo japonês que significa "a prova de erros" engloba os conceitos desenvolvidos por Shingo no Sistema Toyota de Produção durante os anos 60 no Japão. Esses conceitos são aplicados desde o projeto até a implementação dos dispositivos a prova de erros. O objetivo do Poka Yoke é evitar que os erros(humanos, maquina, natureza) se tornem defeitos, através da eliminação de suas causas. Sendo assim, esse sistema, ao evitar que os erros aconteçam, é mais econômico, pois reduz os custos das avaliações e controles da qualidade. Estamos falando então de um controle de qualidade com uma inspeção de 100% já que as causas dos erros são combatidas pelos dispositivos implementados.
Afim de Diminuir significativamente defeitos no produto e evitar retrabalhos, treinamos os colaboradores para que os próprios façam o controle de qualidade em cada etapa do processo de fabricação. Quanto antes for descoberto a falha em um produto, maior será o controle de qualidade do mesmo. Aplicamos o sistema Poka-Yoke, que nos dá uma ajuda para evitar produtos defeituosos.
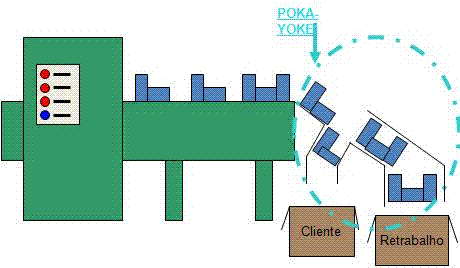
4 – 5S
A filosofia dos 4S busca promover, através da consiência e responsabilidade de todos, disciplica, segurança e produtividade no ambiente de trabalho. Cada uma das cinco palavras representa uma etapa do programa de implementeção do 5S, ou então, como também podem ser chamados os cinco snsos.
- SEITON: Significa deixar tudo em orde, ou o senso organização. É literalmente arrumar tudo, deixar as coisas arrumadas e em seu devido luagar para que seja possível encontrá-las facilmente sempre que necessário. Assim, evita-se o despercício de tempo e energia.
- SEIRI: se refere a evitar o que for desnecessário, ou o “senso de utilização”. Ao separar aquilo que é realmente necessário ao trabalho daquilo que é supérfluo, ou desnecessário, passando-o para outros que possam fazer uso dele ou simplesmente descartando, conseguimos melhorar a arrumação e dar lugar ao novo.
- SEISO: significa manter limpo, ou o “senso de limpeza”. Agora que você já tirou tudo que era desnecessário e deixou tudo em ordem, é preciso manter assim.
- SEIKETSU: zelar pela saúde e higiene, ou “senso de saúde e higiene”. Não adianta nada mantermos o local de trabalho limpo se não cuidarmos de nossa higiene pessoal também.
- SHITSUKE: disciplina. Este conceito é um pouco mais abrangente do que o significado ao qual estamos acostumados de seguir as normas. Ele se refere também ao caráter do indivíduo que deve ser honrado, educado e manter bons hábitos.
Parece bem simples, mas na verdade os 5S são baseados na filosofia japonesa do Bushido (lê-se bushidô). Um código de princípios morais não escritos, mas que foram passados de geração para geração e incorporados à cultura japonesa e que se resumem em disciplina e harmonia.
Durante a década de 60 e 60 os japoneses passaram pela fase de reestruturação do pós-guerra e desenvolvimento acelerado de suas indústrias. Foi nesta fase que começaram a se desenvolver os conceitos de qualidade aplicada aos processos produtivos e, a filosofia dos 5S se espalhou pelo mundo dando origem a novas metodologias (“housekeeping”, por exemplo).
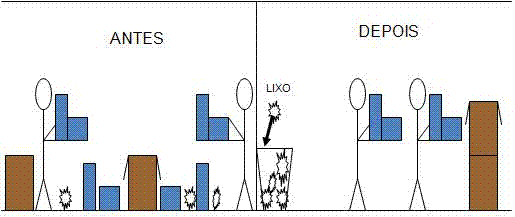
5 – Gestão Visual
Apresentar para todos da empresa visualmente através de gráficos e dados, os resultados e a evolução de cada setor da empresa, motivando-os e deixando-os todos a par da situação da empresa.
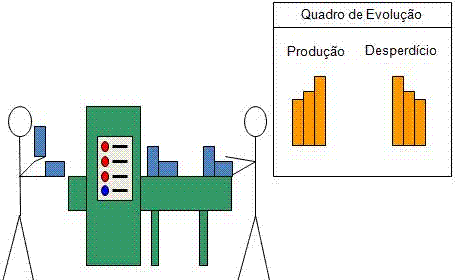
6- Trabalho Padronizado
Muitas empresas sofrem com a variedade de seus produtos, para evitar confusões ou sofrer com a falta de algum colaborador que é especialista em um setor, padronizamos ou deixamos os processos mais fáceis e(ou) mais semelhante uns dos outros. Assim será fácil o deslocamento de um colaborador de um setor para outro, evitando alguns erros na produção.
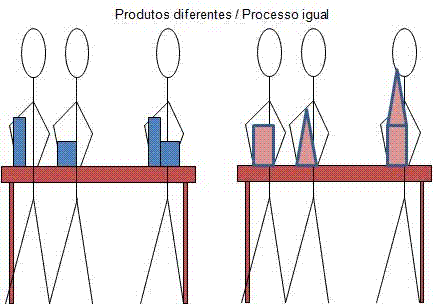
7- SMED Redução do Setup
Basicamente criado para diminuir o tempo do setup das máquinas, geralmente as máquinas são configuradas para uma produção muito grande, gerando uma produção alta e um estoque muito alto, causando um desperdício de espaço e escondendo alguns erros na produção.
Mar de Estoque
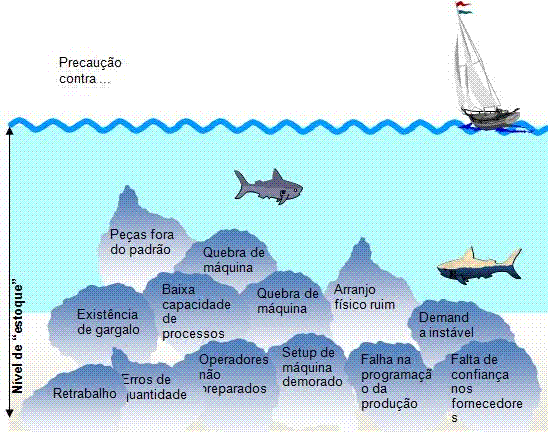
8- Redução da dimensão do Lote
Grandes lotes de matéria prima e de produtos acabados, são causas de grandes desperdícios de espaço, o acúmulo de produtos com datas de validade vencidas, quebras de produtos por colocar caixas sobre caixas, quebra de produtos na movimentação das mesmas. O JIT, ou seja, Just in Time, consiste em produzir somente o necessário, nada em excesso.
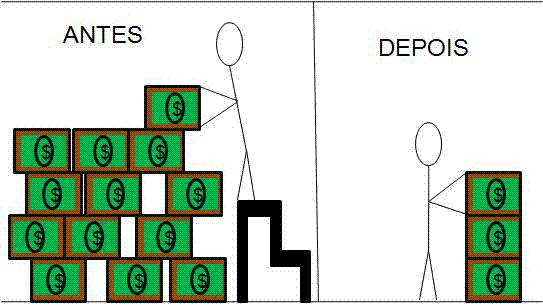
9- Produção Celular (em fluxo contínuo)
Ajustando corretamente os setup das máquinas e aliando-os, normalmente no formato em U, podemos ter um único funcionário dedicado para operar todas as máquinas.

10- Takt time Balanceamento da produção
Estabelecer através de cálculos o ritmo e a quantidade certa que será produzido, normalmente encontrado em linhas de produções contínuas que produzam uma única família de produtos ou similares.
Tt=T/D
Tt = Takt Time ( ritmo da produção)
T = Tempo da produção
D = Procura em unidades durante o período de produção
11- Nivelamento e alisamento da produção
Estratégia para redistribuir o volume de cada um dos diferentes produtos ao longo do tempo e assim extinguindo os extremos máximos e mínimos.
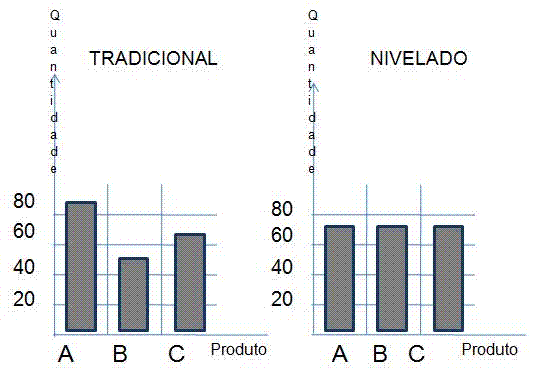
12- Sistemas
Com simples medidas podemos melhorar e muito a produção e o fluxo de pessoas dentro das fábricas, podemos colocar ferramentas próximos dos operadores para facilitar todo o processo de fabricação, dessa mesma forma teremos um ambiente mais organizados. É muito comum encontrarmos uma redução superior a 90% ou mais no número de viagens dos funcionários dentro da fábrica, economizando muito tempo e fadiga.
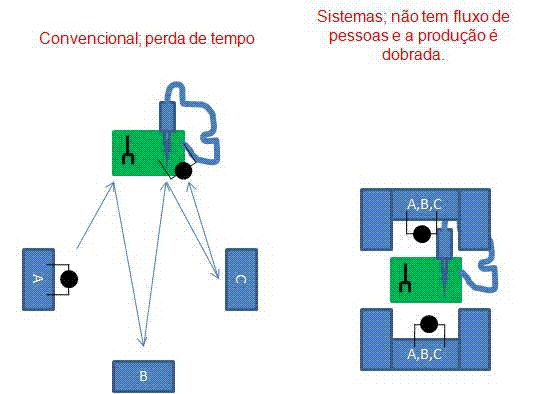
13- Kanban
Conhecido como sistema puxado, facilita a produção e a organização. Sua eficácia é garantida para pequenos lotes e sistemas balanceadas. Um Kanbané uma autorização para produzir ou parar a produção e também pode conter informações sobre cliente e(ou) produto.
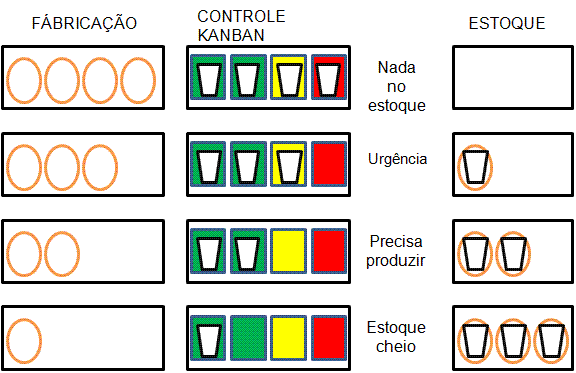
14- Kaizen Melhoria contínua
Através do conhecimento dos 8 desperdícios e das 14 ferramentas do LeanManufecturing, temos que manter o melhoramento contínuo, é muito importante a participação de todos os integrantes da empresa, dos altos e baixos escalões. Kaizen é a procura diária pela perfeição, mantém sempre a equipe motivada e unida.